Understanding how to calculate the torque of a balsa plane project is crucial for achieving optimal performance and flight characteristics. Accurate torque calculations ensure the propeller’s rotational force aligns with the motor’s capabilities, preventing motor burnout or insufficient thrust. This involves considering several factors, including the propeller’s dimensions, the motor’s specifications, and the overall design of the aircraft. Neglecting these calculations can lead to poor flight performance or even catastrophic failure. Precise calculations contribute significantly to a successful balsa wood aircraft project. This article provides a comprehensive guide to this critical aspect of model aircraft design.
The torque produced by a motor in a balsa wood airplane directly impacts the propeller’s ability to generate thrust. Insufficient torque will result in a lack of power, hindering the plane’s ability to take off or climb. Conversely, excessive torque can overload the motor and potentially damage its components. Therefore, careful consideration of the relationship between motor torque, propeller size and pitch, and the overall weight of the aircraft is necessary for successful flight. Understanding this relationship facilitates the selection of appropriate components and ensures efficient energy conversion. The process involves applying basic physics principles to the specific characteristics of the chosen components.
Propeller design plays a significant role in determining torque requirements. A larger propeller diameter generally requires more torque to achieve the same rotational speed compared to a smaller propeller. Similarly, a higher propeller pitch demands greater torque to overcome the increased resistance. The chosen propeller must be compatible with the motor’s torque output to ensure optimal performance. Matching these parameters requires careful consideration of the available motor options and their specifications. The calculations presented below provide a structured approach to this essential task.
Beyond propeller selection, the weight of the aircraft itself is a crucial factor affecting torque needs. A heavier aircraft requires more thrust to achieve lift-off and sustained flight. This increased thrust requirement necessitates a motor with higher torque output, emphasizing the interconnectedness of all components. Precise weight estimation throughout the design process is therefore crucial for accurate torque calculations. Ignoring aircraft weight during these calculations can lead to significant performance deficiencies.
How to Calculate the Torque of a Balsa Plane Project?
Calculating the torque required for a balsa wood airplane project involves understanding the relationship between the motor, propeller, and the aircraft’s overall weight and design. This calculation isn’t an exact science, as several factors influence flight performance, but a well-informed estimate helps avoid common design pitfalls. The process relies on fundamental physics principles and the specific characteristics of the chosen motor and propeller. This detailed approach ensures a balanced design with the appropriate power delivery system. Precise calculations lead to optimal flight performance and minimize the risk of mechanical failure.
-
Determine Propeller Characteristics:
Identify the propeller’s diameter (D) and pitch (P) in inches. These values are usually specified by the manufacturer. The pitch represents the theoretical distance the propeller would advance in one revolution. Accurate measurements are critical for the subsequent calculations.
-
Obtain Motor Specifications:
Consult the motor’s datasheet to find its no-load RPM (revolutions per minute) and the maximum current it can safely handle. These specifications will be crucial for estimating the torque the motor can generate.
-
Calculate Propeller Thrust:
Several empirical formulas exist for estimating propeller thrust. These typically involve the propeller’s diameter, pitch, and rotational speed. One common approach utilizes the power coefficient, requiring additional information, but these often rely on motor-specific data.
-
Estimate Aircraft Weight:
Determine the total weight of the completed aircraft, including the motor, battery, airframe, and any additional components. Accurate weight estimation is vital for calculating the necessary thrust to overcome gravity.
-
Calculate Required Torque:
Using the estimated thrust and propeller characteristics, calculate the required torque using the formula: Torque (oz-in) = (Thrust (oz) * Propeller Radius (in)). This simple formula provides a basic estimate of the torque needed for lift-off and sustained flight.
-
Compare Calculated Torque with Motor Specifications:
Compare the calculated torque with the motor’s rated torque. If the calculated torque exceeds the motor’s capabilities, a more powerful motor or a different propeller may be necessary. This step is crucial to prevent motor overload and potential damage.
Tips for Accurate Torque Calculations
While the above steps provide a basic framework, several refinements can improve the accuracy of torque calculations. Taking into account factors often overlooked can lead to significant improvements in flight performance and reliability. Paying attention to these details significantly increases the chances of a successful project. Using readily available online resources can help refine calculations.
Remember that these calculations provide estimations, not precise values. Flight testing and adjustments will likely be required to fine-tune the performance of the aircraft.
-
Consider Air Density:
Air density varies with altitude and temperature, affecting propeller efficiency. Adjust calculations based on the expected flight conditions.
-
Account for Propeller Efficiency:
Propeller efficiency is rarely 100%. Incorporate a correction factor to account for losses due to friction and other inefficiencies.
-
Use Motor Efficiency Data:
Motor datasheets often include efficiency curves. Using these curves can provide a more accurate estimation of the motor’s actual torque output.
-
Factor in Gear Ratios (if applicable):
If a gearbox is used to reduce the motor’s RPM, incorporate the gear ratio into the torque calculations to account for the mechanical advantage.
-
Iterative Design Process:
Designing and building a model aircraft is often an iterative process. Use the initial calculations as a starting point and refine the design based on testing and observations.
-
Consult Online Resources and Calculators:
Numerous online resources and calculators are available to assist with propeller selection and torque calculations. These tools can simplify the process and provide additional insights.
-
Safety Margin:
Always include a safety margin to account for unforeseen factors and ensure the motor isn’t operating at its absolute maximum capacity.
Accurate torque calculations are essential for efficient flight performance. Insufficient torque results in poor climb rates and limited flight duration, while excessive torque might lead to motor overheating and failure. Understanding these aspects is crucial for optimizing the aircraft’s design. Careful consideration of all relevant factors ensures a successful flight outcome.
The relationship between motor torque, propeller selection, and aircraft weight is complex. Optimizing this relationship requires a thorough understanding of the principles of aerodynamics and power transmission. By carefully considering these interconnected factors, designers can create a balanced and efficient model aircraft.
Remember, these calculations are estimations and serve as a valuable guide, not a definitive answer. Trial and error, coupled with iterative refinements based on testing, are crucial for achieving the desired flight performance. Utilizing this approach, designers can build successful and efficient balsa wood aircraft.
Frequently Asked Questions
Understanding the intricacies of torque calculations in balsa plane design can be challenging. The following questions address common concerns and provide clarification on specific aspects of the process. Addressing these common concerns clarifies the process and empowers designers to make informed decisions.
Q1: What happens if I underestimate the required torque?
Underestimating the required torque can lead to insufficient thrust, resulting in poor climb performance, difficulty taking off, and potentially an inability to sustain level flight. The aircraft might struggle to overcome its weight and air resistance.
Q2: What are the consequences of overestimating the torque?
Overestimating the torque might lead to selecting an excessively powerful motor, resulting in unnecessary weight and increased expense. While not immediately detrimental, it represents inefficient design and potentially places unnecessary strain on other aircraft components.
Q3: How do I account for wind conditions in my calculations?
Wind conditions significantly influence flight performance. While not directly incorporated into the torque calculations, wind necessitates adjustments during flight testing and fine-tuning of the aircraft’s controls.
Q4: Can I use online calculators to assist with my calculations?
Yes, numerous online calculators are available to assist with propeller selection and torque estimation. These calculators often incorporate more complex formulas and can provide helpful guidance.
Q5: How important is the accuracy of the weight estimation?
Accurate weight estimation is crucial because the required thrust is directly proportional to the aircraft’s weight. An inaccurate weight estimation can lead to significant errors in the torque calculation, affecting flight performance.
Q6: What if my calculated torque is significantly different from the motor’s specifications?
A significant discrepancy between the calculated torque and the motor’s specifications indicates a problem with either the calculations, the chosen propeller, or the motor selection. Review all calculations and consider adjusting parameters accordingly.
Successfully calculating the required torque for a balsa wood airplane project is a multifaceted process. It integrates fundamental physics with practical considerations of component selection and aircraft design. Accurate calculations are paramount for achieving efficient and stable flight.
The iterative nature of aircraft design necessitates a continuous process of refinement based on the results of each iteration. The initial calculations provide a valuable starting point, paving the way for a successful flight experience. Careful planning and attention to detail maximize the chances of a successful project.
Therefore, mastering the art of torque calculation is paramount to a successful balsa wood airplane project. It ensures efficient power delivery, prevents motor burnout, and contributes to the overall flight performance and stability of the aircraft. Combining theoretical calculations with practical experimentation yields the optimal flight characteristics.
In conclusion, understanding how to calculate the torque of a balsa plane project is not just about numbers; it’s about comprehending the intricate interplay between various components and ensuring a successful, efficient, and safe flight. Thorough calculations, coupled with a systematic approach and iterative refinements, are essential for realizing the full potential of any balsa wood aircraft project.
Youtube Video Reference:
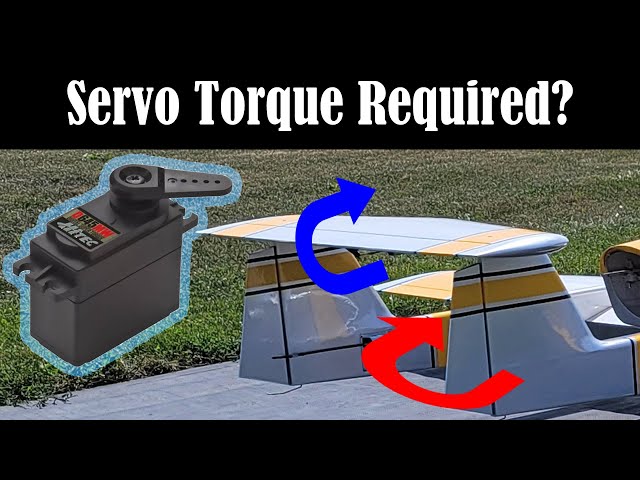